These Japanese traditional crafts are highly valued worldwide for their beauty and advanced techniques. However, few people may accurately understand the differences between Imari and Arita ware. This article will explain in detail the differences between Imari and Arita ware, as well as their history, origins, and production processes.
We’ll explore their respective characteristics and backgrounds, introducing their appeal in a way that’s easy for beginners to understand.
Table of Contents
What are the Differences Between Imari and Arita Ware?
Both Imari and Arita ware are representative traditional Japanese porcelains, primarily produced in Saga Prefecture. While they have a close historical relationship and are often confused, there are several important differences between the two.
Below, we’ll explain these differences in terms of history, production methods, design, raw materials, production areas and distribution, and modern developments.
Differences in Historical Background of Imari and Arita Ware
Arita ware began in 1616 with a group led by Li Sampei, a potter brought from Korea, marking the first production of porcelain in Japan. Using high-quality pottery stone (containing kaolin) discovered by Li Sampei in Izumiyama, Arita, porcelain manufacturing began in Arita town in the former Hizen Province (present-day Saga Prefecture).
On the other hand, the name “Imari ware” originates from these porcelains being exported through the nearby Imari port. During the Edo period, porcelain made in Arita was exported overseas through this port, becoming known internationally as “Imari.” Therefore, historically, Imari and Arita ware often referred to the same thing.
Today, “Imari ware” refers to porcelain made in Imari City and is distinguished from “Arita ware,” though the two are still often confused in modern times.
Differences in Production Methods and Techniques
Arita ware’s production methods include particularly elaborate techniques such as the “Kakiemon style” and “Nabeshima style,” characterized by vivid color paintings on thin, translucent white porcelain. The Kakiemon style, known for its milky white base called “nigoshide” with vibrant paintings primarily in red with additions of blue and green, is especially famous.
Early Imari ware mainly used “sometsuke” or blue and white decoration. This technique involves painting blue patterns on white porcelain using a cobalt-blue pigment called gosu, resulting in simple yet powerful designs. In later periods, colored enamels and kinrande (luxurious gold decorations) were also incorporated, developing more elaborate techniques.
Differences in Design and Decorative Features
Arita ware designs are often intricate and refined, emphasizing compositions that utilize negative space and color balance. The “Kakiemon style,” in particular, is characterized by designs that balance decorativeness with equilibrium, using primarily red colors and leveraging the beauty of negative space.
The “Nabeshima style,” high-grade porcelain made in the clan’s official kilns, is known for its elaborate decorations with attention to detail, used as tribute to the clan and gifts to the shogunate. In contrast, early Imari ware designs primarily featured simple blue “sometsuke” decorations, often depicting animals, plants, or geometric patterns.
Eventually, “colored Imari” emerged with colorful designs, highly valued not only in the domestic market but also as exports to Europe.
Differences in Raw Materials Used
The basic raw materials used in both are almost the same, particularly the “pottery stone (kaolin)” found in Izumiyama, Arita. This high-quality Izumiyama pottery stone gives Arita and Imari ware their characteristic white, hard porcelain body.
However, differences in clay composition, processing methods, firing temperatures, and techniques among various kilns create subtle differences in the texture and color of the finished products.
Differences in Production Areas and Distribution
Regarding production areas, Arita ware is still made in Arita town, Saga Prefecture, while Imari ware is mainly manufactured in Imari City. Historically, porcelain made in Arita was exported through Imari port, hence the name “Imari ware,” but now they are distinguished based on their respective production areas. However, Arita and Imari ware are still often confused in modern times.
In terms of distribution, during the Edo period, Arita ware was mass-produced and exported to Europe through Imari port by the Dutch East India Company. This led to “Imari” being highly valued, especially in Europe. Even today, traces of this remain worldwide, with a particularly established status as high-grade porcelain.
Modern Developments of Imari and Arita Ware
Even in modern times, Arita and Imari ware continue to be highly valued both domestically and internationally. With over 400 years of history, Arita ware still preserves traditional techniques while actively incorporating new designs and technologies. It has established its position as a global ceramic brand, significantly influencing renowned European kilns like Meissen in Germany in the 18th century.
Meanwhile, Imari ware artisans are also preserving traditions while creating products suited to modern lifestyles, producing a wide range of items from everyday tableware to art pieces. New works are also emerging through collaborations with contemporary artists and designers. Furthermore, tours of kilns in Imari and Arita have become popular tourist attractions, drawing many visitors from Japan and abroad.
Thus, Imari and Arita ware, each with its own history and characteristics, continue to be loved both domestically and internationally as representative Japanese porcelains.
History of Imari and Arita Ware
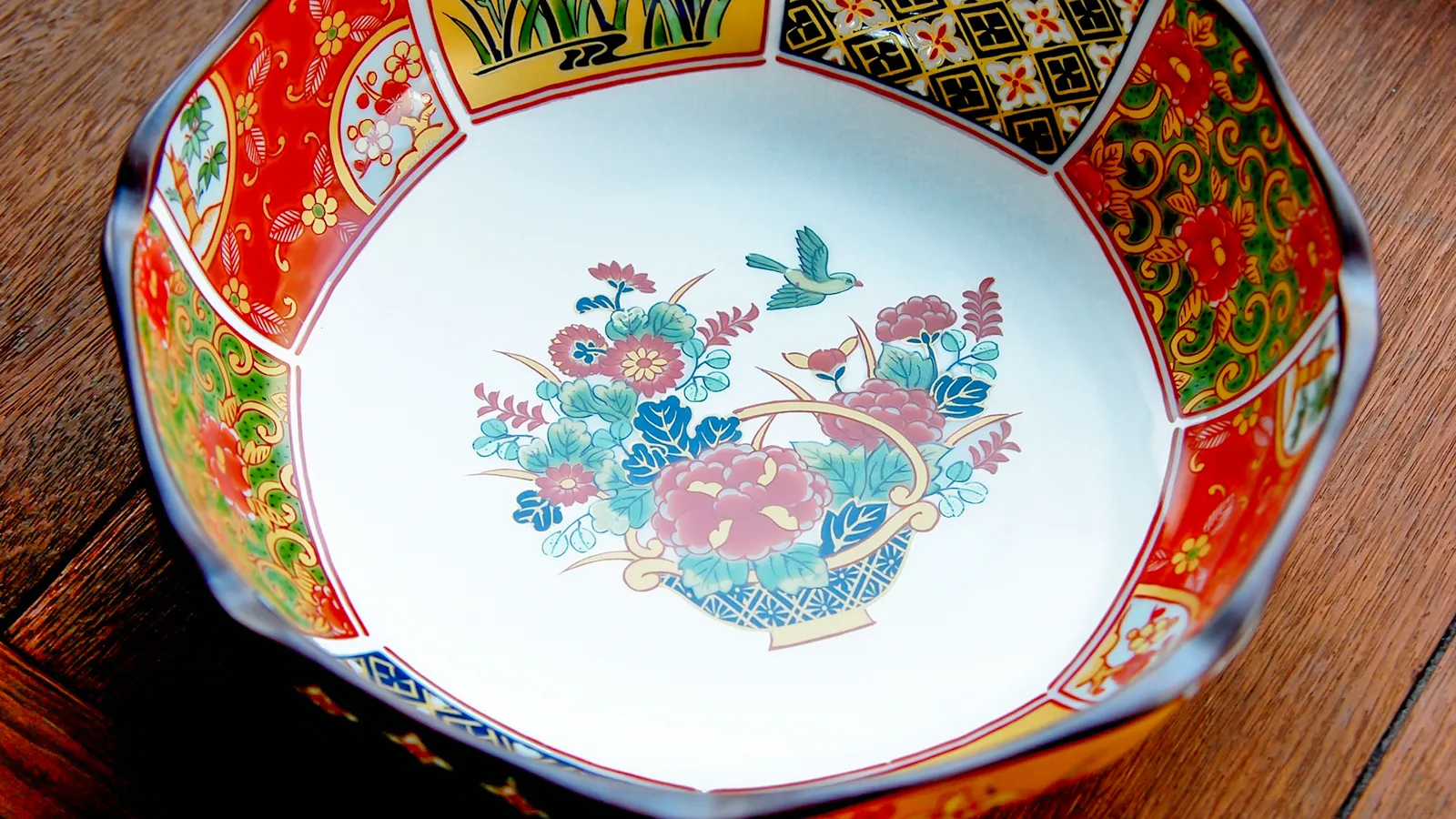
Imari and Arita ware have a long history as representative Japanese porcelains. They have undergone many changes from their birth through development in the Edo period, worldwide fame through exports, to modernization. Here, we’ll take a detailed look at their respective histories and origins.
Birth and Origins of Imari and Arita Ware
The beginning of Arita ware dates back to 1616 when Li Sampei, a potter brought from the Korean Peninsula to Japan, introduced the technique. He discovered high-quality pottery stone (containing kaolin) in Izumiyama, Arita town, Saga Prefecture, and successfully produced porcelain in Japan for the first time using this material.
The name “Imari ware,” on the other hand, originates from porcelain produced in Arita being exported through the nearby Imari port. During the Edo period, Arita ware and Imari ware were used almost synonymously, but in modern times, they are distinguished as “Arita ware” and “Imari ware” based on their respective production areas.
Development of Imari and Arita Ware in the Edo Period
Entering the Edo period, Arita ware made significant progress in both technology and design. While blue and white porcelain was mainstream in the early days, colored enamel techniques such as the “Kakiemon style” and “Nabeshima style” developed in the latter half of the 17th century, leading to the production of porcelain with vibrant colors.
During this time, Arita’s porcelain industry was under the control of the Nabeshima clan, with strict quality control enforced. As a result, the precision and beauty of the products further improved, and Arita ware was also produced as high-grade porcelain for clan use. In particular, the lavish “Nabeshima ware” became renowned for its elegance.
Peak Period as Export Porcelain
From the latter half of the 17th century to the 18th century, Arita ware established international acclaim through exports to Europe. At that time, when porcelain production in Jingdezhen, China, was halted due to the Qing dynasty’s maritime ban policy, Arita ware met the resulting high demand. Particularly, the Dutch East India Company exported large quantities of Arita ware from Imari port, making it widely known as “Imari” among European nobility.
In Europe, Arita ware’s delicate and beautiful white porcelain and vivid colored enamels were highly valued, greatly influencing local porcelain industries, especially the Meissen kiln in Germany.
Technological Innovation and Modernization After the Meiji Era
After the Meiji Restoration, Japan rapidly modernized, and the porcelain industry was also affected. Particularly from the 1870s, its importance as a domestic export industry was re-recognized, leading to technological innovations. With the introduction of steam kilns and the development of more precise painting techniques, Arita ware once again received international recognition through world expositions.
During this period, many designs and products were created for the European market, and influenced by Japonisme, more decorative and vibrant styles were in demand. Simultaneously, domestic demand for porcelain as daily use items increased, leading to the production of many affordable tableware and decorative items.
Journey from Post-War to Modern Times
After World War II, the production of Arita and Imari ware temporarily declined but regained attention with post-war economic recovery. Especially with the recovery of the domestic market, while preserving traditional techniques, simple designs and practical products suited to modern lifestyles were created, increasing demand both domestically and internationally.
Furthermore, in conjunction with the tourism industry, tours visiting kilns in Arita and Imari have become popular, with artisans focusing on training successors and passing down techniques to preserve their traditions for future generations. Additionally, contemporary artists and designers are creating works that add new creativity to traditional techniques, increasing appreciation as art pieces.
The Influence of Imari and Arita Ware on the World
Arita ware, with its beauty and high level of craftsmanship, greatly influenced the European porcelain industry. Export items known as “Imari ware” were highly valued among European nobility from the 17th to 18th centuries, contributing to the development of the European porcelain industry.
Even today, Arita ware continues innovative efforts while preserving traditions, receiving high acclaim in various countries worldwide. For instance, numerous works are housed in museums in Europe and America, displayed in institutions like the Metropolitan Museum of Art and the British Museum. Arita and Imari ware continue to shine on the international stage as symbols of Japanese culture, loved worldwide while inheriting their history and traditions.
Production Methods of Imari and Arita Ware
The production of Imari and Arita ware involves traditional techniques developed over centuries. The production process is highly precise, involving many stages to completion.
Here, we’ll look in detail at each process from shaping to firing and painting.
Shaping Techniques and Tools Used
In shaping Imari and Arita ware, traditional methods such as hand-building and wheel-throwing continue to be used today. Wheel-throwing, in particular, is an important process that requires the artisan’s advanced skills.
Using a wheel allows for uniform thickness of the vessels and creates smooth curves and intricate shapes, producing thin and light porcelain. The main tools used in shaping are as follows:
Potter’s Wheel
A tool used to shape the basic form of vessels by uniformly forming clay rotated at high speed. The rotation speed and hand pressure greatly affect the thickness and shape of the vessel.
Spatulas and Planes
Tools used to smooth the surface of the shaped vessel, removing excess clay to smoothen the form and create fine details.
Molds (wooden or plaster)
Often used for specific shapes or mass production, these help form the basic shape of vessels or vases.
Using these tools, artisans create various products such as vessels, plates, and vases while making minute adjustments. The process of creating works with attention to detail while preserving traditional techniques is truly a testament to the artisans’ skills and experience.
Bisque Firing and Main Firing Processes
After shaping is complete, the work is dried and then undergoes “bisque firing.” Bisque firing is done to stabilize the shape of the vessel and ensure even application of glaze, fired at about 850-900°C.
This process completely removes moisture from the clay, making the vessel easier to handle and forming the basic shape of the porcelain. After this, glaze is applied, followed by “main firing.”
Main firing is done at about 1300°C, resulting in porcelain with a glass-like surface that is hard and highly water-resistant. The high-temperature firing causes the clay components to melt together, resulting in whiter and harder vessels. The higher the firing temperature, the more the porcelain crystallizes, increasing its strength and beauty, making this the most crucial finishing stage.
Types of Glazes and Glazing Methods
Glazes create a glass-like film on the surface of porcelain, serving both decorative and functional roles. Various types of glazes are used in Arita and Imari ware, but mainly “transparent glaze” and “milky white glaze” are common. Transparent glaze brings out the whiteness of the porcelain, while milky white glaze creates a soft color tone.
Glazing (the process of applying glaze) includes the following methods:
- Dipping: A method of covering the entire work by immersing it in glaze. Suitable for applying glaze uniformly.
- Brush Application: A method of applying glaze using a brush. Effective for applying glaze to detailed areas.
- Spraying: A method of spraying glaze. Easy to adjust concentration and achieve uniform finish.
This process is carried out very carefully, as inaccurate glazing can result in unevenness after firing.
Painting Process and Traditional Techniques
The beauty of Arita and Imari ware lies in their intricate paintings. Painting is broadly divided into two categories: “sometsuke” (blue and white) and “iroe” (colored enamels).
Sometsuke is a technique of painting blue patterns on white porcelain using gosu (cobalt pigment). It is painted under the glaze and develops a beautiful blue color after firing. This technique developed under the influence of Chinese blue and white porcelain in the 17th century.
On the other hand, iroe involves applying overglaze enamels in red, green, blue, gold, etc., after glazing, followed by a second low-temperature firing. In Arita, colored enamel techniques were introduced in the 1640s, enabling luxurious and colorful decorations through overglaze painting.
Painting is done by hand by artisans, with intricate brushwork depicting animals, plants, and landscapes. Particularly famous styles include the “Kakiemon style,” characterized by red-based designs, and the “Nabeshima style,” known for its luxurious decorations.
The Kakiemon style is characterized by red paintings that stand out against a milky white base (nigoshide). The Nabeshima style, produced in strictly managed clan kilns, is known as high-quality decorative porcelain.
Types of Kilns and Firing Techniques
Various types of kilns are used for firing, from the traditional “climbing kiln” to modern “gas kilns” and “electric kilns.”
A climbing kiln is a multi-chamber kiln built along a hillside, characterized by its ability to fire a large number of works at once in multiple firing chambers. It uses wood as fuel and requires long firing periods of 30-50 hours, but the natural ash fall acts like a glaze, creating a unique texture.
However, adjusting temperature and oxygen levels during firing is difficult and requires traditional skills, but the resulting works have a distinctive, deep flavor unique to wood-fired kilns.
On the other hand, gas and electric kilns are modern kilns that allow for easy temperature control and precise firing. They are particularly valuable for cases requiring fine temperature adjustments, such as the main firing of colored enamels.
Gas and electric kilns enable stable quality and uniform firing due to the type of fuel and usage method, and are widely used in modern porcelain production. Unlike traditional climbing kilns, these kilns allow for shorter firing times but often result in a different finish from the unique texture of climbing kilns.
Importance of Quality Control and Finishing
Finally, the fired works are carefully inspected. Artisans rigorously check for cracks, chips, color unevenness, warping, and glaze irregularities, and defective items are removed. Furthermore, to enhance the beauty of the work, decorations such as polishing and gold painting are applied for the final finish.
The quality of Arita and Imari ware is highly valued worldwide, and quality control is carried out while preserving traditional techniques and incorporating modern technological innovations. Through this process, the highest quality porcelain is completed.
The production process of Imari and Arita ware is supported by the artisans’ skills and meticulous management. While traditional techniques are still alive, innovations to meet modern needs are also being advanced, and their beauty and functionality continue to attract attention worldwide as one of the most notable crafts.
Summary
Imari and Arita ware, as representative Japanese porcelains, have over 400 years of history and tradition. Arita ware originated in 1616 when porcelain was first produced in Japan, and is particularly known for its vibrant and intricate colored enamel techniques such as the “Kakiemon style” and “Nabeshima style.” On the other hand, the name “Imari ware” derives from these porcelains being exported from Imari port, and is widely known in Europe as “Imari.”
Even in modern times, Imari and Arita ware continue to be loved both domestically and internationally, preserving their traditions while incorporating contemporary designs and technological innovations. Their refined designs and high functionality cater to a wide range of uses, from everyday tableware to art pieces, and their appeal is likely to continue in the future.